Recycling Produced & Flowback Wastewater for Fracking Operations
Hydraulic fracturing is performed at depths between 5,000 - 20,000 feet and requires 100,000 - 500,000 barrels of water (4.2 to 21 million gallons) per well. The water is mixed with 0.5% (by volume) of various chemical additives, including crosslinked gelling agents and friction reducers to increase the water's flow and deposition efficiency, a function of rheology. Fracturing utilizes highly pressurized fluids between 2,000 - 8,000 psi at an average flow rate of 2000 gpm (47 bbl/min). These fluids must be slick enough to carry proppant (sand grains and/or ceramic beads) into micro-fissures in the rock formation to keep them open and enable the release of the formation resource.
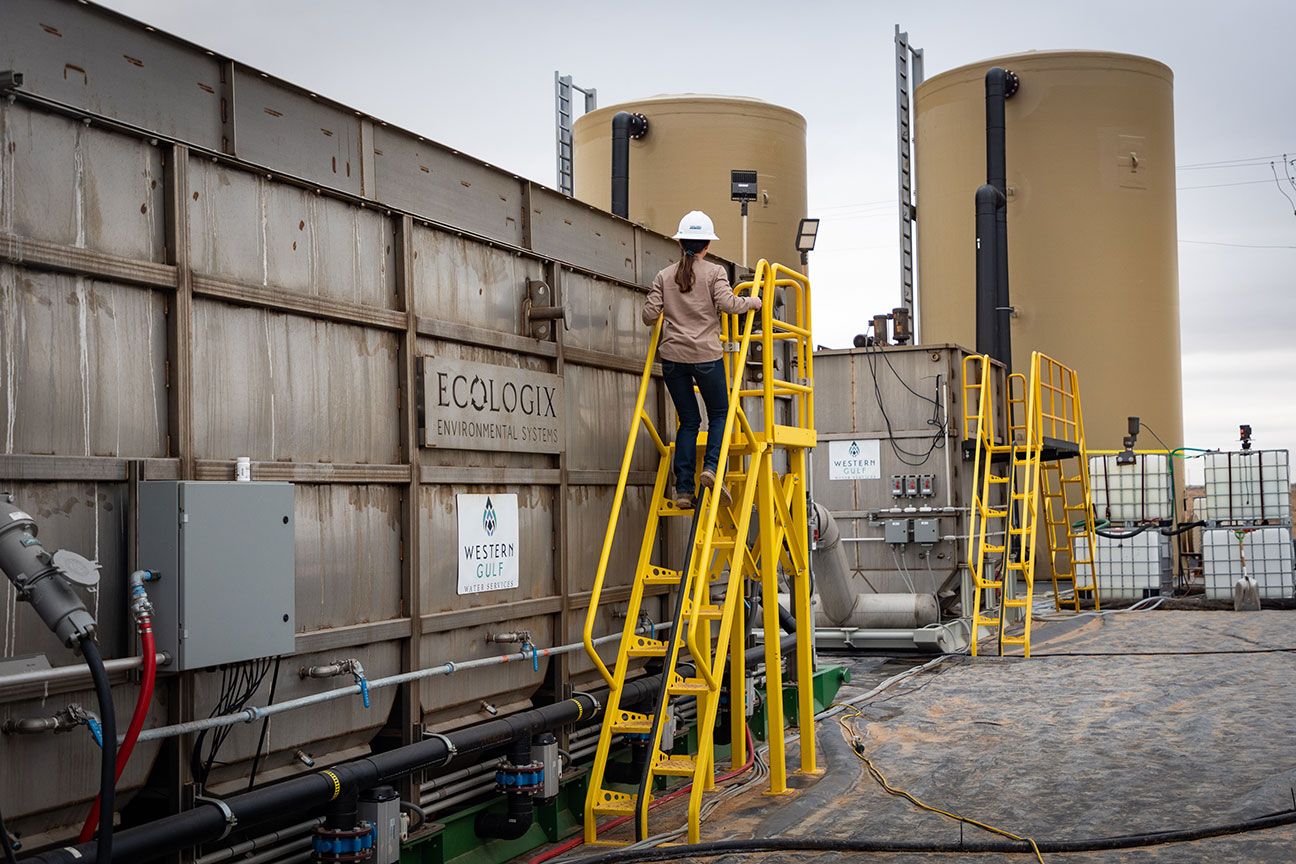
A 2013 publication1 from the Society of Petroleum Engineers (SPE) details a study, conducted by Halliburton and XTO Energy, which concludes that produced water with TDS (Total Dissolved Solids) levels as high as 285,000 mg/L (28.5% salinity) was shown to generate proper crosslinked rheology for hydraulic fracturing in line with wells that were fracturing with just 20,000 ppm (2% salinity). In the field study a mixture of common drilling chemicals such as Carboxymethyl Hydroxypropyl Guar Gum (CMHPG) (a zirconium-based cross- linker, sodium chlorite breakers, and non-emulsified surfactants), were blended with 100% treated produced water to generate a frac fluid that performed as well as that expected from a fluid based on fresh water. The fluids were used to complete seven wells in New Mexico's Delaware basin.
The study shows that brine water possesses all the characteristics required for effective fracking: easy preparation, rapid hydration, low fluid loss, good proppant transport capacity, low pipe friction, and effective recovery from the reservoir. Unlike fresh water, salt water does not restrict oil flow because of an osmotic imbalance that results in clay swelling. Simply put, salt water is good for fracking and any statements other- wise are unfounded.
The same study indicates that in addition to preserving fresh water for agricultural and commercial use, employing produced water for fracking can help reduce approximately 1400 truckloads from the roads, and all but eliminate the use of disposal wells. As a result, the study delivered a $70,000 - $100,000 cost savings per well.
However, the study did not go far enough to address other related issues. Why does the oil industry continue to operate on the assumption that water with high levels of TDS is unsuitable for fracking? The perceived understanding has always been that salty water prevents the proper hydration of the crosslink-gel and friction reducers, but as this study indicates - salt is clearly not the issue. Is there something else that would prevent a proper hydration of guar gum in the water?
The real reason that the oil industry prefers to use fresh water for fracking is simply because it is cheap and clean, completely justifiable when trying to run a business. In essence, it is the low count of Total Suspended Solids (TSS) in aquifer water that makes the gelling hydration possible, not the absence of salt.
The fact is, that TSS in the form of colloidal particles are very small in size (0.001 to 1 micron), yet very large in surface area. This structure makes colloids abrasive friction inducers, negatively impacting the rheology of crosslinked gels. Where the oil industry has long operated on the notion that TDS is the bottleneck in widespread frac water reuse, the study shows that TSS is the real culprit.
Understanding Frac Fluid Composition
Frac fluids are blended to a level that is viscous enough to effectively transport the proppant, yet slick enough to permeate micro-fissures in the rock formations. The chemicals used to maintain this balance are commonly called gelling agents and friction reducers. In the overall composition of frac fluids, these specific chemicals generally account for less than 0.1% by volume (see Figure 1). But even at such a small concentration, these chemicals play a vitally important role in ensuring that the frac fluids are effective at carrying the proppant into the formation to keep fissures open.
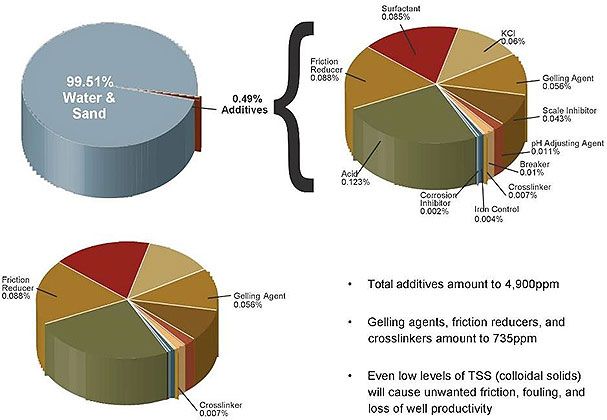
The bench test results shown below in Table 1 indicate removal rates in the treated produced water. Most parameters underwent a minor change after treatment, except for TSS, turbidity and iron, which saw dramatic reductions. The study recounts that at 99% TSS removal, the produced water was success- fully blended into a crosslinked-gel-based frac fluid suitable for hydraulic fracturing.
Suspended solids come in various shapes and sizes; removing the visible range of solids, the ones that contribute to turbidity, is insufficient when it comes to frac fluid mixology. Extending beyond an 85% reduction in TSS to a 99% reduction is largely a matter of colloidal solids removal. These particles are not easily filtered, nor do they rapidly settle out of a solution. The only way to remove them is through the chemical means of charge neutralization, followed by physical separation process.
Parameter | Raw Sample | Treated Sample | % Change |
---|---|---|---|
pH | 4.83 | 8.00 | |
Conductivity, μS/cm | 257 | 258 | +0.39 |
Chloride, mg/L | 163,637 | 164,951 | +0.80 |
Sodium | 70,342 | 75,517 | +7.36 |
Calcium | 29,222 | 28,845 | +1.29 |
Magnesium | 4,347 | 3,148 | -27.58 |
Strontium | 2,204 | 2,020 | -8.39 |
Potassium | 1,660 | 1,689 | +1.75 |
Boron | 20.3 | 16.6 | -18.28 |
Sulfate | 40 | 38 | +5.00 |
Barium | 5.69 | 6.03 | +5.98 |
TDS | 267,588 | 273,552 | +2.23 |
Iron | 34.6 | 0.26 | -99.25 |
Turbidity, NTU | 182 | 15.4 | -91.54 |
TSS | 10,623 | 92 | -99.13 |
With regards to frac fluid rheology, the effect of colloidal particles can be explained with a simple illustration. A puddle of motor oil on the floor is slippery – to keep from slipping, you toss some sand over it. The sand creates friction and the oil is no longer slippery. Colloidal solids in frac fluid act the same way, however, their introduction to the mix has a negative effect in the fracking context. A very low concentration of guar gum and polyacrylamide help carry the proppant into the stimulated fractures. Even the smallest amount of colloidal solids present in the fluid will create unwanted friction and negate the effect of the chemicals.
As Figure 1 illustrates, 0.49% of additives amount to 4,900 parts per million (ppm). The collective amount of gelling agents, friction reducers and crosslinkers add up to 15% of the total additives, or 735 ppm. Thus, even a small amount of TSS will cause friction, fouling and other undesirable effects.
The reality is, the key factor to high quality water for fracking is the removal of TSS, not TDS. This new understanding enables the use of any brine water - including produced water - for fracking purposes.
Conclusion
The discussions on whether high TDS concentrations restrict frac water reuse in future fracking operations can be put to rest. Both the laboratory and field results of the study in the cited article demonstrate that it is feasible to use treated produced water as a basis for crosslinked- gel-based hydraulic fracturing. As a bonus, several other benefits were realized:
- Brine water can effectively replace fresh water in the frac fluid mixture
- Fresh water resources can be left untouched in the fracking process
- Trucking requirements for water transport can be cut by hundreds of loads per well
- Savings can add up to $100,000 per well
- Using brine water will prevent clay from swelling, resulting in higher well productivity
With the outlook of water consumption in the industry hanging in the balance, the scientific evidence that produced water can be reused repeatedly through a long series of wells is a beacon of hope. Environmental opposition to the practice of withdrawing fresh water from aquifers, rivers, and lakes can be averted by repurposing the water that's already in our possession. It's a story that we've been communicating for a long time - frac water must be reused. Opting to use fresh water is simply the wrong move, because now we know with irrefutable evidence, TSS removal is the key to frac water reuse.
The industry should focus on best practices to remove TSS and the technologies that are best suited for this task. One such option is the mobile Integrated Treatment System (ITS-1500) by Ecologix Environ- mental Systems, capable of processing up to 1500 gpm or 51,000 bbl/day with up to 99% TSS removal.
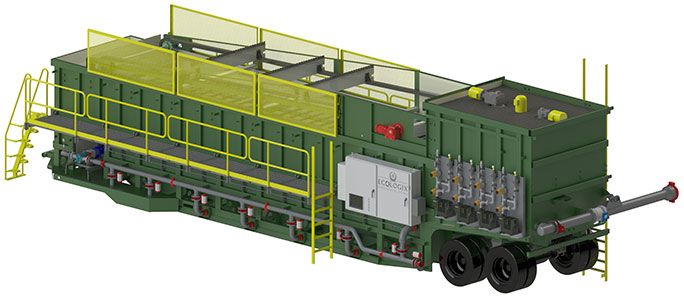
About Ecologix
Ecologix Environmental Systems is an Atlanta-based wastewater treatment company specializing in the Oil and Gas Industry. Ecologix has a proprietary mobile, Integrated Treatment System (ITS) for frac water treatment that can remove up to 99% of TSS at flow rates up to 1500gpm (51,000 BPD). Also, the portable DAF model E-825 is capable of processing up to 1900gpm (66,000 BPD) and the E-1040 can process up to 3700gpm (127,000 BPD).
1 Lebas, R. et al. “Development and Use of High-TDS Recycled Produced Water for Crosslinked-Gel-Based Hydraulic Fracturing” SPE 163824. Feb 2013.